
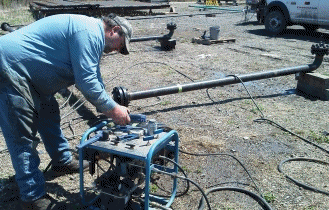
Pipeline & Compressor
Pipe Fabrication
Pipeline & Compressor Station Pipe Fabrication
Contractor Feedback: "This was the cleanest fabrication I ever dealt with. In the entire project, there was only one spool that needed adjusted on site. I definitely plan to work with FaberFab for all future pipeline fabrication jobs."
Project Summary: FaberFab worked as a sub-contractor to the pipeline contractor on this project to fabricate all the launchers, receivers, headers and risers. The project consisted of three pipelines connecting to a compressor station. The pipelines were 10", 12" and 16" pipe size, pipe materials ranged from API-5L to API-X65. The project took eleven weeks from the arrival of the first truck load of pipe and fittings until the last painted pipe spool was loaded on the pipeline contractors truck.
FaberFab was able to add value to the project by:
- Using its large yard and facility to efficiently stage and check in material
- Doing a CAD layout of the piping system to determine accurate pipe cut lengths resulting in excellent field fit ups
- Operating an organized manufacturing process where each cut pipe and component was easily identifiable by all persons working on the project
- Efficient execution of all roll out welds on the weld manipulator to minimize per weld times
- Using in-house electro hydraulic bolt up machines to minimize bolt up labor
- Using in-house hydrostatic pressure test equipment and personnel to reduce hydrostatic pressure test lead times
- Saving shipping costs due to facilities close proximity to the job sites
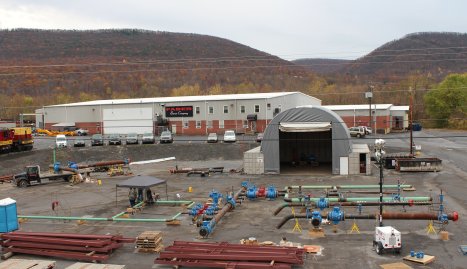
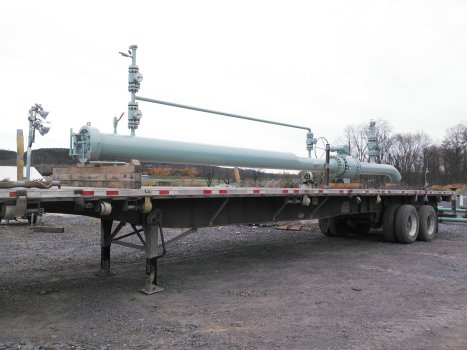
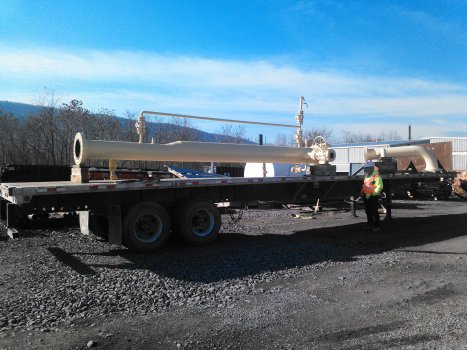
Scope of project for this mid-stream gathering included:
- Receiving and staging materials
- CAD layout of piping to determine and cut pipe lengths
- Completing 775 welds, pipe sized from 2" to 20"
- Maintain welder ID and X-Ray map quality control documents
- Two 16" launchers
- Two 12" launchers
- Two 10" launchers
- 10", 12" and 16" headers, distribution system and risers
- Bolt up of all valves and pipe spools
- 8 hour hydrostatic tests to 2200 PSI
- Disassembled, sand blasted, primed and painted to specified colors
- Loaded on trucks, with delivery provided by contractor.
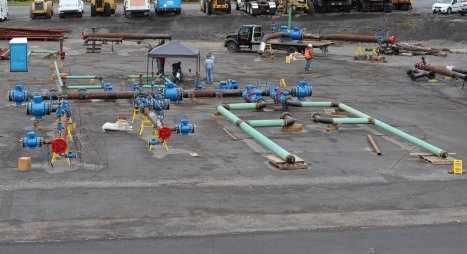
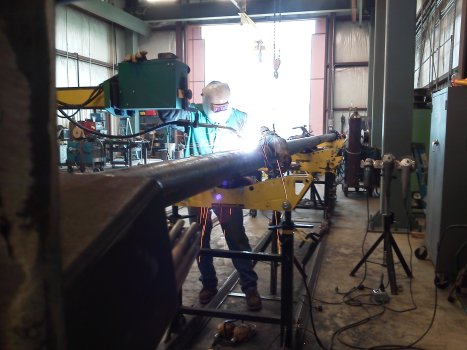

© 2019 FaberFab
1000 East Bald Eagle Street | Lock Haven, PA 17745
570.748.4009 | info@faberfab.com